Robotic structural integrity evaluation uses advanced drones and sensors to assess the physical condition of industrial structures and equipment. You'll find it's an essential process for maintaining safety and preventing costly failures. These robotic systems can access hazardous or hard-to-reach areas, reducing human risk while providing highly accurate data. They employ various sensors and imaging technologies to detect defects, corrosion, and structural weaknesses. With AI and machine learning integration, the evaluation process becomes faster and more precise than traditional methods. The benefits of this cutting-edge approach extend across multiple industries, promising a safer and more efficient future for structural inspections.
Key Takeaways
- Robotic structural integrity evaluation assesses a robot's ability to maintain its physical form and functionality under various stresses.
- It involves examining material strength, load-bearing capacity, and environmental resistance to prevent deformation, breakage, or failure during operation.
- The evaluation considers static and dynamic forces, vibrations, and repetitive motions that can lead to fatigue over time.
- It encompasses the entire lifecycle of a robot, from design to long-term durability, ensuring reliable performance throughout its operational lifespan.
- Regular evaluations identify wear, fatigue, or damage before catastrophic failures occur, safeguarding both the robot and the entire operation.
Definition of Robotic Structural Integrity
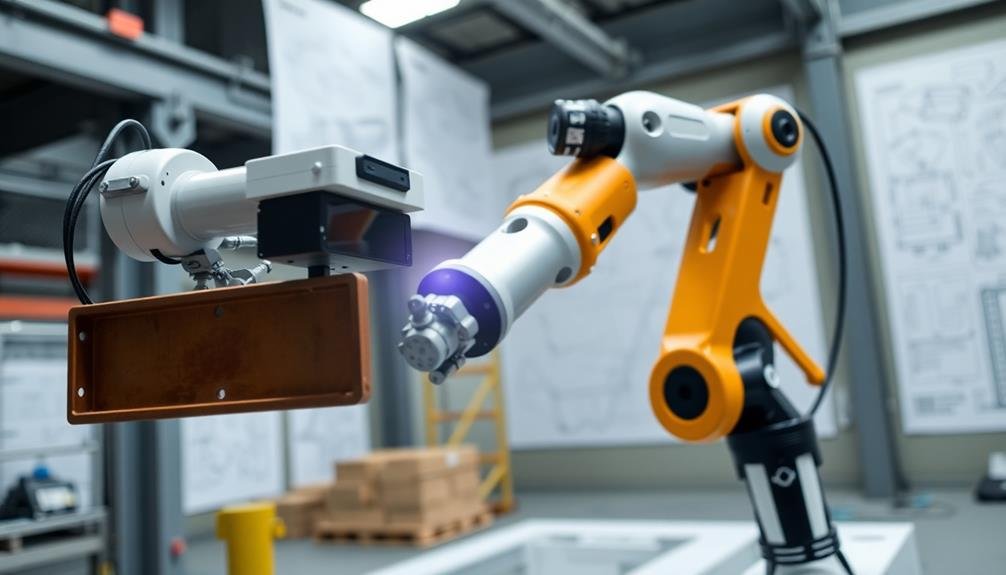
Structural integrity lies at the heart of robotic design and functionality. When you're dealing with robotic structural integrity, you're focusing on a robot's ability to maintain its physical form and perform its intended functions under various conditions and stresses.
It's about ensuring that every component, from the frame to the joints and actuators, can withstand the forces they'll encounter during operation. You'll need to evaluate factors like material strength, load-bearing capacity, and resistance to environmental factors.
A robot with good structural integrity won't deform, break, or fail when subjected to expected operational stresses. This includes withstanding its own weight, carrying payloads, and resisting external forces.
It's not just about static strength, though. You must also account for dynamic forces, vibrations, and repetitive motions that can lead to fatigue over time.
Robotic structural integrity encompasses the entire lifecycle of the machine, from initial design to long-term durability. By prioritizing structural integrity, you're ensuring that your robot can perform reliably, safely, and efficiently in its intended role, whether that's in manufacturing, healthcare, or exploration.
Importance in Industrial Inspections

When you're evaluating robotic structural integrity in industrial settings, you're not just safeguarding the robot itself—you're protecting an entire operation.
Industrial inspections rely heavily on robotic systems to perform tasks in hazardous or hard-to-reach areas. If these robots fail due to structural issues, it can lead to costly downtime, safety risks, and potential damage to the facility or products.
Regular integrity evaluations help you identify wear and tear, fatigue, or damage before they cause catastrophic failures. This proactive approach allows you to schedule maintenance during planned downtimes, minimizing disruptions to your production schedule.
You'll also extend the lifespan of your robotic assets, maximizing your return on investment.
Moreover, robotic structural integrity is essential for maintaining safety standards. In industries like nuclear power, oil and gas, or chemical processing, a robot's failure could expose workers to dangerous environments or substances.
Types of Drones Used

You'll encounter three main types of drones in structural integrity evaluations: fixed-wing inspection drones, multirotor structural assessment UAVs, and hybrid VTOL platforms.
Each type offers unique advantages for different inspection scenarios. Understanding these drone categories will help you choose the most suitable option for your specific structural evaluation needs.
Fixed-Wing Inspection Drones
Among the various types of drones used for structural inspections, fixed-wing models stand out for their efficiency in covering large areas. These drones resemble small airplanes and are designed for long-range flights, making them ideal for inspecting expansive structures like bridges, pipelines, and power lines.
You'll find that fixed-wing inspection drones offer several advantages. They can stay airborne for extended periods, often flying for hours on a single battery charge. This extended flight time allows you to collect more data in a single mission, reducing the need for multiple flights.
Fixed-wing drones also excel at capturing high-resolution imagery and can be equipped with various sensors, including thermal cameras and LiDAR systems.
When you're inspecting large-scale infrastructure, fixed-wing drones can provide a thorough overview of the entire structure. They're particularly useful for identifying areas that require closer inspection, which you can then follow up with multirotor drones for detailed analysis.
However, it's essential to recognize that fixed-wing drones typically require more space for takeoff and landing, and they're less maneuverable in tight spaces compared to their multirotor counterparts.
Multirotor Structural Assessment UAVS
In contrast to fixed-wing models, multirotor structural assessment UAVs offer unparalleled maneuverability for close-up inspections. These drones can hover in place, fly sideways, and even navigate through tight spaces, making them ideal for examining complex structures.
You'll find multirotor UAVs equipped with high-resolution cameras, thermal imaging sensors, and LiDAR technology to capture detailed data about a structure's condition.
When using multirotor drones for structural assessments, you'll benefit from their ability to:
- Perform vertical takeoffs and landings in confined spaces
- Maintain stable flight in windy conditions
- Capture images and data from multiple angles without changing position
Multirotor UAVs come in various configurations, typically with four, six, or eight rotors. The more rotors a drone has, the greater its stability and payload capacity.
This allows for the integration of advanced sensors and equipment necessary for thorough structural evaluations. You'll find these drones particularly useful for inspecting tall buildings, bridges, and other hard-to-reach structures where traditional methods might be dangerous or time-consuming.
Hybrid VTOL Platforms
Hybrid VTOL (Vertical Takeoff and Landing) platforms combine the best features of both fixed-wing and multirotor drones, offering a versatile solution for structural integrity evaluations. These drones can take off and land vertically like multirotors, but they also have fixed wings that allow for efficient forward flight. This unique design enables them to cover larger areas and fly for longer durations compared to traditional multirotor drones.
You'll find that hybrid VTOL platforms are particularly useful for inspecting large structures such as bridges, dams, and tall buildings. They can hover in place to capture detailed images of specific areas, then quickly shift to forward flight to move between inspection points. This flexibility allows you to conduct thorough structural assessments more efficiently.
When using a hybrid VTOL platform, you'll benefit from its increased payload capacity, which allows for the integration of advanced sensors and cameras. You can equip these drones with thermal imaging cameras, LiDAR sensors, and high-resolution cameras to gather a wide range of data about the structure's condition.
The extended flight time also means you can complete more extensive inspections in a single mission, reducing the need for multiple flights and saving time in the field.
Sensors and Imaging Technologies
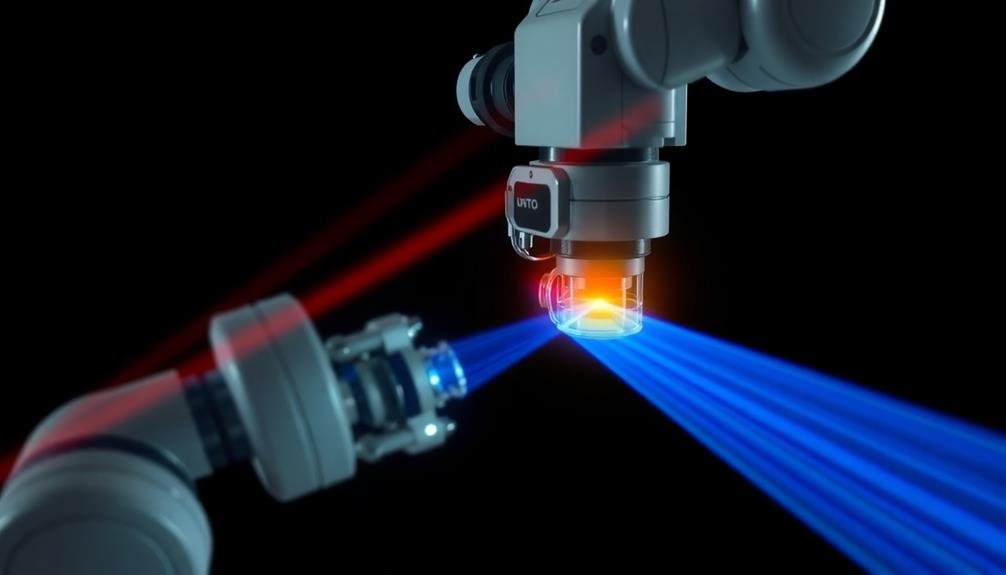
Cutting-edge sensors and imaging technologies form the backbone of robotic structural integrity evaluation systems.
These advanced tools allow you to detect and analyze structural defects with unprecedented accuracy and efficiency. You'll find that modern robotic systems employ a wide array of sensors, including ultrasonic, infrared, and electromagnetic sensors, to gather extensive data about a structure's condition.
Imaging technologies play an essential role in visualizing and interpreting the data collected by sensors.
You'll be amazed at how high-resolution cameras, 3D scanners, and thermal imaging devices can reveal hidden flaws and potential weak points in structures. These technologies enable you to create detailed digital models of the inspected structures, making it easier to identify and track issues over time.
Here's a quick overview of the key benefits you'll gain from using advanced sensors and imaging technologies:
- Enhanced detection of microscopic defects
- Real-time data analysis and visualization
- Improved accuracy in predicting structural failures
Data Collection Techniques
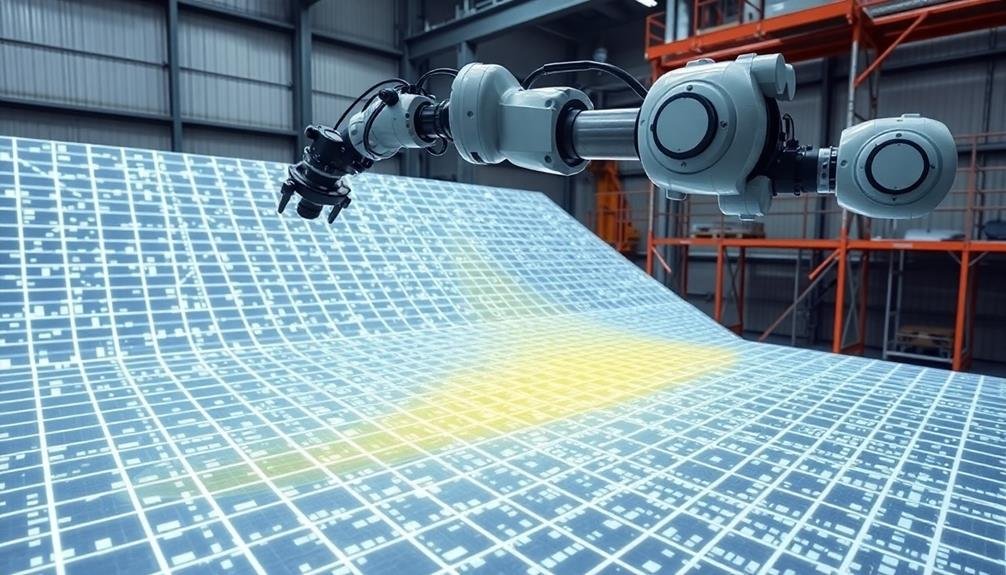
You'll find that data collection for robotic structural integrity evaluation relies on three primary techniques.
Sensor-based data acquisition systems gather real-time information on structural conditions, while visual inspection methods employ cameras and image processing to detect surface anomalies.
Additionally, you can use non-destructive testing techniques like ultrasound or X-ray imaging to examine internal structures without causing damage.
Sensor-Based Data Acquisition
Robotic inspection systems rely heavily on sensor-based data acquisition for effective structural integrity evaluation. These systems use various sensors to collect data about the structure's condition, allowing for accurate assessment without human intervention.
You'll find that sensor-based data acquisition offers several advantages over traditional manual inspection methods, including increased precision, consistency, and the ability to access hard-to-reach areas.
When implementing sensor-based data acquisition in robotic structural integrity evaluation, you'll typically use a combination of different sensor types:
- Visual sensors: Cameras and LiDAR systems for capturing images and 3D scans
- Non-destructive testing (NDT) sensors: Ultrasonic, eddy current, and infrared sensors for detecting internal defects
- Environmental sensors: Temperature, humidity, and vibration sensors for monitoring ambient conditions
Visual Inspection Methods
Visual inspection methods form the cornerstone of data collection techniques in robotic structural integrity evaluation. These methods use advanced imaging technologies to capture detailed visual data of structures.
You'll find that robots equipped with high-resolution cameras can scan surfaces for cracks, corrosion, or other signs of damage that might be invisible to the naked eye.
Infrared thermography is another powerful visual inspection tool. It allows you to detect temperature variations that might indicate structural weaknesses or hidden defects.
You can also employ laser scanning techniques, which create precise 3D models of structures, enabling you to identify deformations or irregularities.
Underwater structures aren't off-limits either. Robots with specialized cameras and lighting can perform visual inspections in challenging aquatic environments.
You'll even find drones being used for aerial inspections of tall structures or hard-to-reach areas.
Machine learning algorithms are increasingly being integrated into these visual inspection methods. They can analyze image data in real-time, flagging potential issues for further investigation.
This combination of robotic visual inspection and AI is revolutionizing the field of structural integrity evaluation, making it faster, more accurate, and more thorough than ever before.
Non-Destructive Testing Techniques
Numerous non-destructive testing (NDT) techniques complement visual inspection methods in robotic structural integrity evaluation.
These advanced methods allow you to assess a structure's condition without causing damage. You'll find that NDT techniques are essential for detecting hidden flaws, measuring material properties, and evaluating structural integrity in hard-to-reach areas.
When conducting robotic structural integrity evaluations, you can employ various NDT techniques:
- Ultrasonic testing: Use high-frequency sound waves to detect internal defects and measure material thickness.
- Radiographic testing: Utilize X-rays or gamma rays to create images of internal structures, revealing hidden flaws.
- Eddy current testing: Apply electromagnetic fields to detect surface and near-surface defects in conductive materials.
Structural Analysis Methods
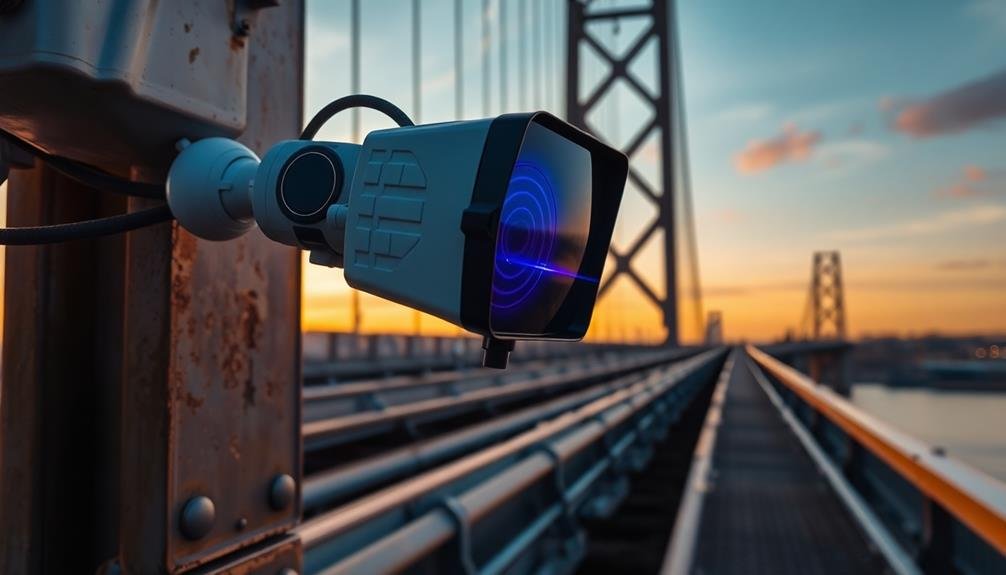
In the domain of robotic structural integrity evaluation, engineers rely on a variety of analytical techniques to assess a structure's soundness. You'll find that these methods range from computer simulations to physical load tests. Finite Element Analysis (FEA) is a popular approach, where you'll break down complex structures into smaller, more manageable elements for detailed examination.
You'll also encounter modal analysis, which helps you understand a structure's vibrational characteristics. This method's particularly useful for identifying potential resonance issues. Stress analysis is another critical technique you'll use to determine how a structure responds to various loads and pressures.
Here's a quick overview of common structural analysis methods:
Method | Application | Pros | Cons |
---|---|---|---|
FEA | Complex geometries | Detailed results | Computationally intensive |
Modal Analysis | Vibration studies | Identifies resonances | Limited to linear systems |
Stress Analysis | Load-bearing structures | Predicts failure points | Simplifies material properties |
Fatigue Analysis | Cyclic loading | Long-term predictions | Requires extensive data |
AI and Machine Learning Integration

Technological evolution has ushered in a new era of structural integrity evaluation through AI and machine learning integration. You'll find that these advanced technologies are revolutionizing how robotic systems assess and analyze structural health.
By incorporating AI algorithms and machine learning models, you're able to process vast amounts of data quickly and accurately, leading to more precise evaluations and predictions.
AI and machine learning integration in robotic structural integrity evaluation offers several key benefits:
- Predictive maintenance: AI models can forecast potential structural failures before they occur, allowing for proactive repairs.
- Real-time analysis: Machine learning algorithms can process sensor data in real-time, providing instant insights into structural health.
- Pattern recognition: AI systems can identify subtle patterns and anomalies that human inspectors might miss, improving overall assessment accuracy.
You'll notice that these technologies enable your robotic systems to learn from past evaluations, continuously improving their accuracy and efficiency.
As you integrate AI and machine learning into your structural integrity evaluation processes, you're not only enhancing the capabilities of your robotic systems but also considerably reducing the risk of structural failures and associated costs.
Advantages Over Traditional Inspections
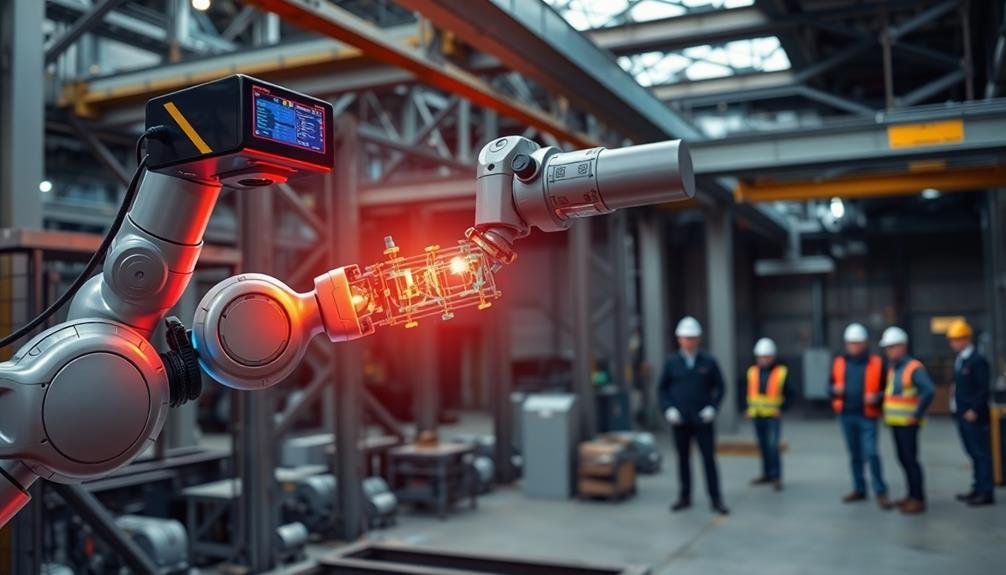
You'll find that robotic structural integrity evaluations offer significant advantages over traditional inspection methods.
These systems provide increased accuracy and precision while completing inspections much faster than human counterparts.
Furthermore, robots can access hazardous areas, reducing risks to human inspectors and enabling more thorough evaluations of structures.
Increased Accuracy and Precision
When it relates to structural integrity evaluations, robotic systems offer a significant leap forward in accuracy and precision compared to traditional inspection methods.
These advanced systems use cutting-edge sensors and imaging technologies to detect even the tiniest flaws or inconsistencies in structures. You'll find that robotic inspections can identify issues that might be missed by human inspectors, ensuring a more thorough evaluation of structural integrity.
Robotic systems excel in providing consistent and repeatable results, eliminating the variability often associated with human-led inspections. They can perform measurements with extreme precision, down to fractions of a millimeter, giving you highly reliable data for analysis.
This increased accuracy translates to better decision-making when it comes to maintenance, repairs, and safety assessments.
Here are three key advantages of robotic systems regarding accuracy and precision:
- Advanced sensors capable of detecting microscopic defects
- Consistent performance without fatigue or human error
- High-resolution imaging and 3D mapping for detailed structural analysis
With robotic structural integrity evaluations, you're investing in a technology that provides unparalleled accuracy, ensuring the safety and longevity of your structures.
Faster Inspection Processes
In addition to enhanced accuracy, robotic structural integrity evaluations offer significant time savings over traditional inspection methods.
You'll find that robots can work continuously without fatigue, completing inspections much faster than human inspectors. They can cover large areas quickly, accessing hard-to-reach places with ease.
Robotic systems can simultaneously collect and process data, eliminating the need for separate analysis steps. This real-time processing allows for immediate identification of potential issues, speeding up the overall inspection process.
You'll also benefit from automated reporting features that generate detailed inspection reports instantly, reducing the time spent on paperwork.
Moreover, you can program robots to follow optimized inspection routes, ensuring efficient coverage of the entire structure. They don't need breaks or rest periods, allowing for 24/7 operation if necessary.
This continuous inspection capability is particularly valuable in time-sensitive situations or when monitoring critical infrastructure.
Access to Hazardous Areas
Robotic inspection systems offer a significant advantage when it comes to accessing hazardous areas. These machines can enter environments that are too dangerous for human inspectors, such as areas with toxic chemicals, extreme temperatures, or high radiation levels.
You'll find that robots can navigate through tight spaces, climb vertical surfaces, and even operate underwater, allowing for extensive structural evaluations in previously inaccessible locations.
By using robotic systems, you're not only protecting human workers from potential harm but also gaining access to critical information about structures in hazardous zones. These robots can be equipped with various sensors and cameras to collect data and transmit it in real-time to operators in safe locations.
This capability enables you to:
- Assess structural integrity in nuclear power plants
- Inspect offshore oil rigs and underwater pipelines
- Evaluate damage in disaster-stricken areas
With robotic inspection systems, you're no longer limited by human physical constraints or safety concerns. You can now perform thorough evaluations of structures in hazardous environments, ensuring the safety and reliability of critical infrastructure while minimizing risks to human personnel.
Challenges and Limitations
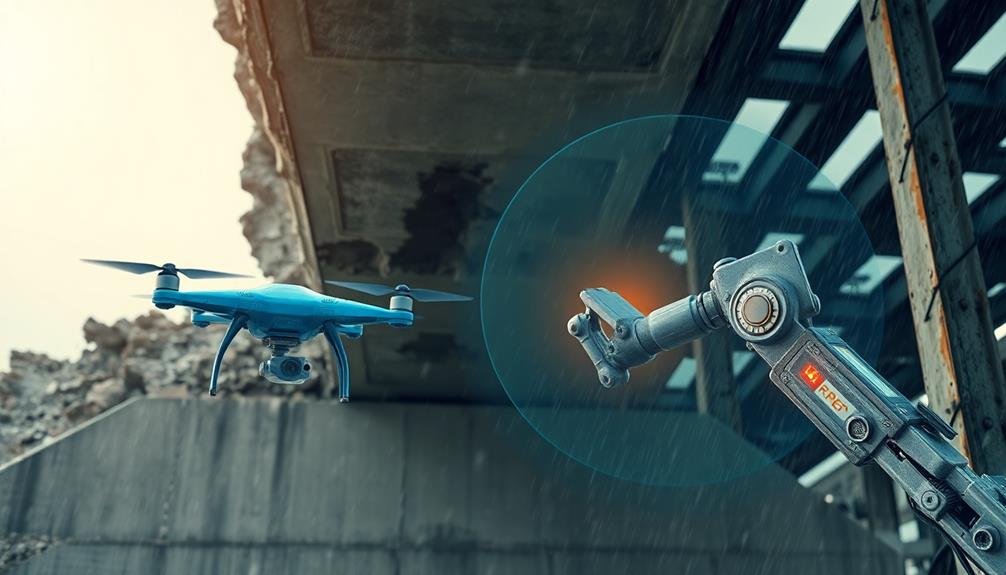
Complexity poses a significant challenge in robotic structural integrity evaluation. You'll find that intricate structures with numerous components and varying materials can be difficult for robots to assess accurately.
Robots may struggle to navigate complex geometries or identify subtle defects in these environments.
Environmental factors also present obstacles. You're likely to encounter issues with lighting, temperature, and humidity that can affect sensor performance and data accuracy.
In outdoor settings, wind and precipitation can further complicate robotic inspections.
Data interpretation remains a challenge. While robots excel at collecting vast amounts of data, you'll need sophisticated algorithms and human expertise to analyze and make sense of this information effectively.
Battery life and power management limit the operational time of robotic systems. You'll need to plan inspections carefully to guarantee complete coverage before recharging is necessary.
Regulatory compliance and safety standards can restrict the use of robotic systems in certain industries or locations. You'll need to navigate these regulations carefully when implementing robotic evaluation methods.
Lastly, the high initial cost of robotic systems may deter some organizations from adopting this technology, despite its long-term benefits.
Safety Considerations
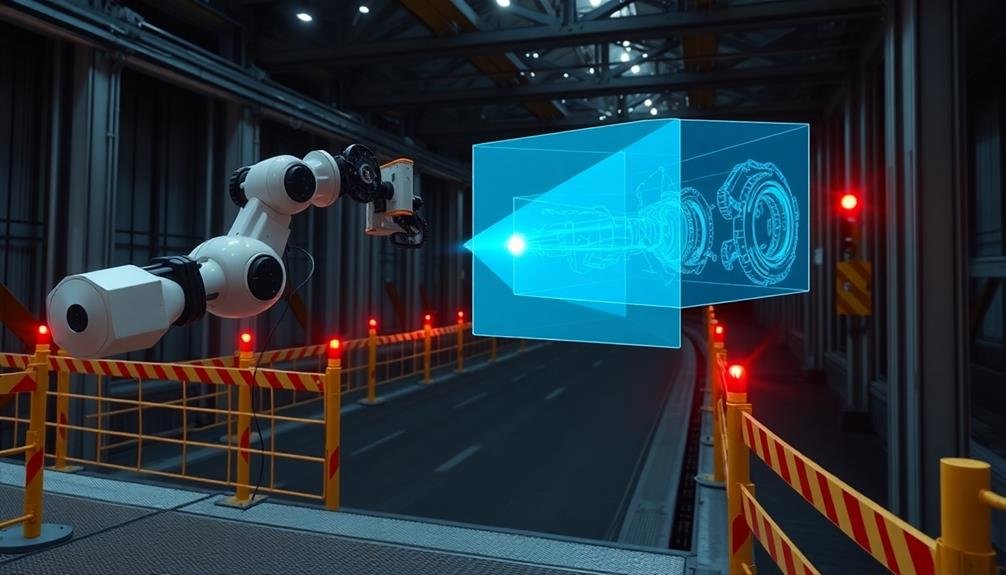
When implementing robotic structural integrity evaluation systems, you'll need to establish extensive risk assessment protocols to identify potential hazards.
It's vital to develop and test emergency shutdown procedures to prevent accidents and minimize damage in case of system failures.
You must also guarantee that operators receive thorough training on safety measures, equipment handling, and proper response to various scenarios.
Risk Assessment Protocols
How can we guarantee the safety of robotic structural integrity evaluation systems? To ascertain the safety of these advanced systems, you'll need to implement thorough risk assessment protocols.
These protocols are essential for identifying potential hazards, evaluating their likelihood and severity, and developing mitigation strategies.
When conducting a risk assessment for robotic structural integrity evaluation systems, you should focus on three key areas:
- System functionality: Assess the robot's mechanical components, sensors, and control systems for potential failure points or malfunctions.
- Environmental factors: Evaluate the operating environment for potential hazards, including physical obstacles, weather conditions, and human interactions.
- Data integrity: Analyze the system's data collection, processing, and reporting mechanisms to ascertain accurate and reliable results.
Emergency Shutdown Procedures
Building on the foundation of risk assessment protocols, it's imperative to establish robust emergency shutdown procedures for robotic structural integrity evaluation systems. You'll need to implement a multi-tiered approach that guarantees quick and effective responses to potential hazards.
First, you must identify critical triggers that warrant an emergency shutdown. These can include sensor anomalies, unexpected robotic behavior, or environmental factors. Next, you'll want to design a clear chain of command for initiating shutdowns, guaranteeing that both human operators and automated systems can respond swiftly.
Consider incorporating the following emergency shutdown components:
Component | Function | Activation Method |
---|---|---|
Kill switch | Immediate power cut | Manual button press |
Software halt | Controlled stop | Remote command |
Failsafe mechanism | Mechanical brake | Automatic sensor trigger |
You'll need to regularly test and update these procedures to maintain their effectiveness. Conduct drills to familiarize your team with the shutdown process and refine it based on real-world scenarios. Remember, a well-executed emergency shutdown can prevent catastrophic failures and protect both personnel and equipment. By prioritizing these safety measures, you'll enhance the overall reliability and trustworthiness of your robotic structural integrity evaluation system.
Operator Training Requirements
To guarantee the safe operation of robotic structural integrity evaluation systems, thorough operator training is essential. You'll need to complete extensive training programs that cover both theoretical knowledge and hands-on experience. These programs should include detailed instruction on the system's components, operating procedures, and safety protocols.
You must master the following key areas:
- System functionality and limitations
- Data interpretation and analysis techniques
- Emergency response and troubleshooting
You'll learn to calibrate sensors, program inspection routines, and interpret complex data outputs. It's vital that you understand how to identify potential structural issues and make informed decisions based on the evaluation results.
You'll also need to familiarize yourself with relevant industry standards and regulations. Your training should include simulated scenarios to prepare you for real-world challenges.
You'll practice responding to various system malfunctions and emergency situations. Regular refresher courses and updates on new technologies will help you stay current with industry advancements.
Regulatory Compliance

In the domain of robotic structural integrity evaluation, regulatory compliance plays an essential role. You'll need to adhere to various standards and regulations to guarantee your robotic systems meet safety and performance requirements. These guidelines often vary by industry and region, so it's vital to stay informed about the specific rules that apply to your operations.
Key areas of regulatory compliance include:
Area | Description |
---|---|
Safety | Ensuring robots don't pose risks to humans |
Performance | Meeting efficiency and accuracy standards |
Environmental | Adhering to eco-friendly practices |
Data Protection | Safeguarding sensitive information |
You'll need to regularly audit your robotic systems to maintain compliance. This involves documenting procedures, conducting risk assessments, and implementing necessary safeguards. It's also important to train your staff on compliance requirements and keep them updated on any changes.
Cost-Effectiveness of Drone Inspections
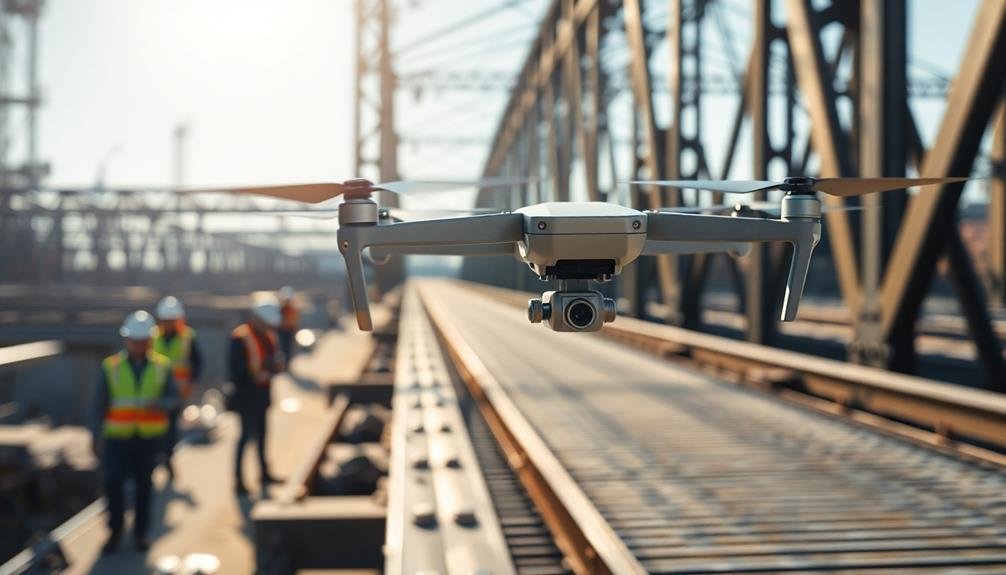
Drones have revolutionized structural integrity evaluations, offering a cost-effective alternative to traditional inspection methods. You'll find that drone inspections considerably reduce labor costs and time spent on-site. They eliminate the need for scaffolding, cranes, or rope access systems, which can be expensive and time-consuming to set up.
Additionally, drones can access hard-to-reach areas quickly and safely, minimizing risks to human inspectors.
When you consider the cost-effectiveness of drone inspections, you'll notice several key benefits:
- Reduced downtime: Drones can inspect structures while they're still operational, minimizing disruptions to business activities.
- Increased frequency: The lower cost allows for more frequent inspections, helping you catch potential issues earlier.
- All-encompassing data collection: Drones capture high-resolution images and videos, providing detailed documentation for analysis and comparison over time.
You'll also appreciate the scalability of drone inspections. Whether you're evaluating a single building or multiple structures across a large area, drones can efficiently cover ground and gather data.
This scalability makes them particularly cost-effective for large-scale projects or ongoing maintenance programs.
Applications Across Various Industries
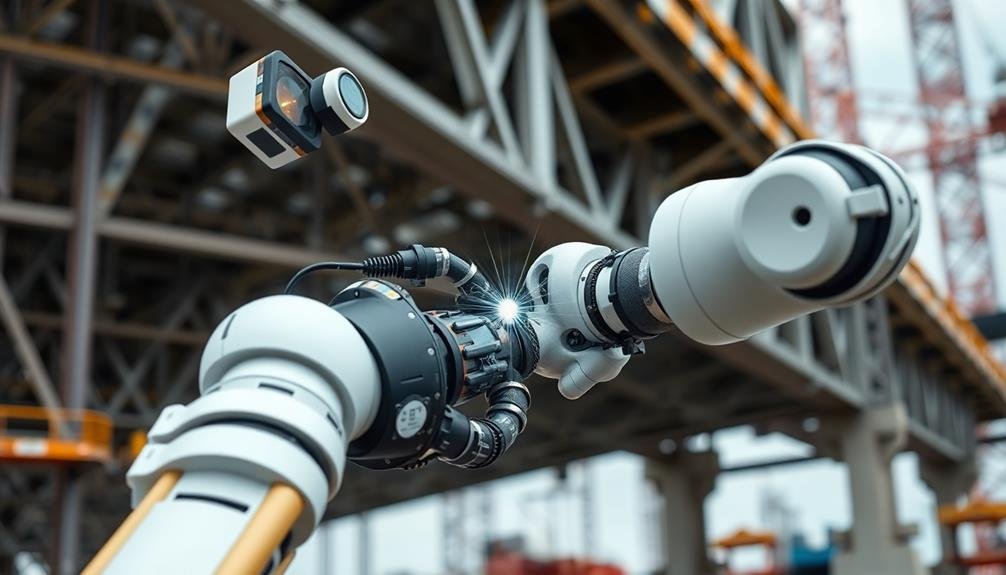
The versatility of robotic structural integrity evaluation extends far beyond a single industry. You'll find these advanced systems at work in sectors ranging from aerospace to civil engineering. In manufacturing, robots inspect complex machinery and production lines, ensuring optimal performance and safety. The oil and gas industry relies on these technologies to examine pipelines and offshore platforms, preventing costly failures and environmental disasters.
Here's a quick overview of applications across various industries:
Industry | Application | Benefits |
---|---|---|
Aerospace | Aircraft fuselage inspection | Enhanced safety, reduced downtime |
Construction | Bridge and building assessment | Early detection of structural issues |
Energy | Wind turbine blade examination | Improved efficiency, longer lifespan |
You'll also see robotic evaluation systems in nuclear power plants, where they inspect reactor vessels and containment structures. In the automotive sector, these robots assess vehicle frames and components for quality control. Even in the domain of cultural heritage, you'll find them examining historical structures to guide preservation efforts. As technology advances, you can expect to see robotic structural integrity evaluation becoming increasingly prevalent across even more industries.
Future Trends and Developments

Looking ahead, you'll see robotic structural integrity evaluation evolving rapidly. As technology advances, these systems will become more sophisticated, offering enhanced capabilities and wider applications. You can expect improvements in sensor technology, data processing, and AI integration, leading to more accurate and efficient evaluations.
Robotics and automation will play an increasingly important role in structural integrity assessments across various industries. You'll witness the development of:
- Swarm robotics for large-scale inspections
- Self-healing materials that can repair minor damages autonomously
- AI-powered predictive maintenance systems
These innovations will revolutionize how you approach structural integrity evaluation. You'll be able to detect potential issues earlier, reduce downtime, and optimize maintenance schedules.
Additionally, you can anticipate the integration of augmented reality and virtual reality technologies, allowing for more intuitive data visualization and remote inspections.
As environmental concerns grow, you'll see a shift towards more sustainable and eco-friendly robotic systems. These developments won't only improve the safety and reliability of structures but also contribute to reducing the overall environmental impact of inspection and maintenance processes.
Frequently Asked Questions
How Long Does It Take to Train Operators for Robotic Structural Integrity Evaluations?
You'll find training times vary based on operator experience and system complexity. It typically takes 2-4 weeks for basic training, but mastering advanced techniques can require several months of hands-on practice and ongoing education.
Can Robotic Inspections Be Conducted in Extreme Weather Conditions?
You'll find that robotic inspections can often handle extreme weather. They're designed for harsh conditions, but there are limits. Heavy rain, strong winds, or extreme temperatures may affect performance or require specialized equipment. Always check manufacturer guidelines.
What Maintenance Is Required for Robotic Inspection Equipment?
You'll need to regularly clean, lubricate, and calibrate your robotic inspection equipment. Don't forget to update software, replace worn parts, and check battery health. Proper storage and careful handling during transport are also essential for longevity.
How Do Robotic Inspections Impact Insurance Premiums for Industrial Facilities?
You'll likely see reduced insurance premiums for your industrial facility when using robotic inspections. They provide more accurate and frequent assessments, lowering risk. Insurers often offer discounts for facilities employing advanced inspection technologies like these.
Are There Any Privacy Concerns Associated With Drone-Based Structural Integrity Evaluations?
You should be aware of privacy concerns with drone-based evaluations. They can capture sensitive data or images unintentionally. It's important to guarantee proper protocols are in place to protect privacy and comply with regulations during inspections.
In Summary
You've explored the world of robotic structural integrity evaluation, a cutting-edge approach to industrial inspections. You've learned about the drones, sensors, and techniques used to collect essential data. You've seen how it guarantees regulatory compliance and cost-effectiveness across various industries. As technology advances, you'll likely witness even more innovative applications in this field. Keep an eye on future developments – they'll shape the way we maintain and inspect structures.
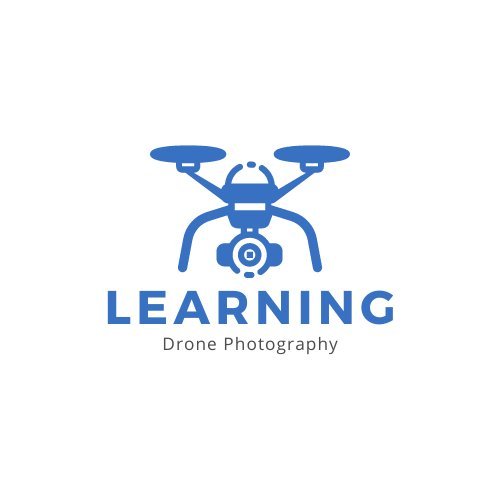
As educators and advocates for responsible drone use, we’re committed to sharing our knowledge and expertise with aspiring aerial photographers.
Leave a Reply