You'll find oil refinery inspections undergoing a dramatic transformation with the advent of high-tech safety solutions. Drones equipped with advanced cameras now perform aerial surveys, accessing hard-to-reach areas and minimizing risks. Thermal imaging detects invisible leaks, while AI-powered systems analyze complex data for faster defect recognition. Real-time data analysis enables predictive maintenance, reducing downtime and preventing accidents. These technologies guarantee regulatory compliance, improve safety, and streamline operations. From robotics to IoT sensors, these innovations are revolutionizing how refineries conduct inspections, making them more efficient, accurate, and cost-effective. Discover how these cutting-edge solutions are reshaping the future of refinery safety.
Key Takeaways
- Drone technology with high-resolution cameras enables quick, comprehensive aerial surveys of refineries, reducing inspection times and costs.
- AI-powered defect recognition systems analyze complex data for faster, more accurate identification of potential issues.
- Thermal imaging detects temperature variations to identify leaks invisible to the naked eye, enhancing safety during inspections.
- Robotics and IoT sensors provide continuous monitoring of equipment health, supporting predictive maintenance and reducing downtime.
- Advanced technologies improve regulatory compliance, prevent accidents, and enhance overall safety management in oil refineries.
Drone Technology in Refinery Inspections
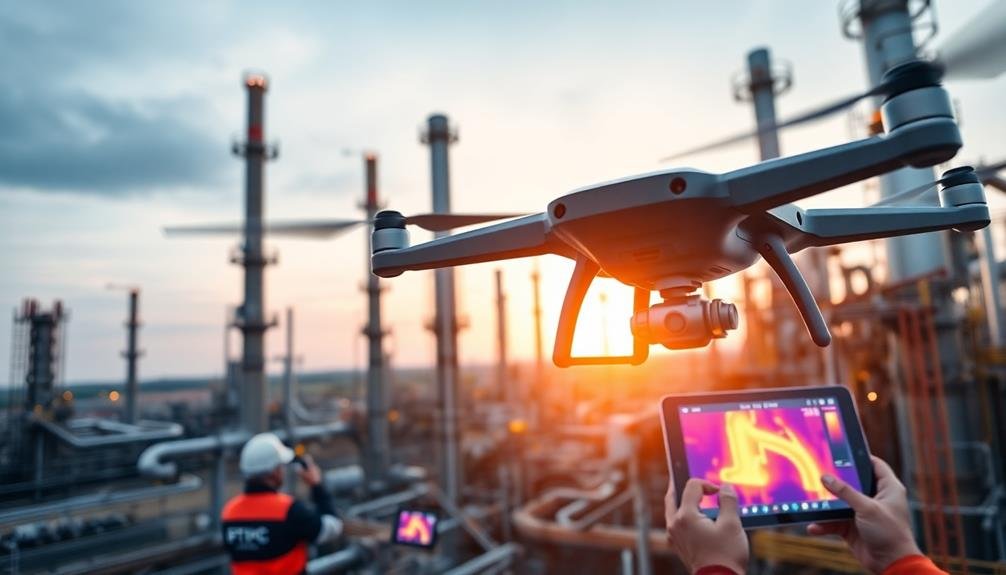
Eyes in the sky are revolutionizing oil refinery inspections. Drones equipped with high-resolution cameras and sensors now offer a safer, more efficient way to monitor vast industrial complexes. You'll find these unmanned aerial vehicles zipping through hard-to-reach areas, capturing detailed imagery of pipelines, storage tanks, and processing units.
Drone technology allows you to conduct thorough inspections without putting workers at risk in hazardous environments. They can easily access elevated structures, confined spaces, and areas with potential chemical exposure. You'll appreciate the real-time data transmission, enabling immediate analysis and decision-making.
These flying robots are also cost-effective. You'll save on scaffolding, lifts, and other equipment typically needed for manual inspections. Drones can cover large areas quickly, reducing downtime and increasing productivity.
Advanced software enhances drone capabilities, offering features like thermal imaging to detect heat anomalies, gas sensors to identify leaks, and 3D mapping for precise structural analysis. You can even program autonomous flight paths for regular, standardized inspections.
As regulations evolve, you'll find drones becoming an integral part of refinery safety protocols, complementing traditional inspection methods and enhancing overall plant integrity.
Benefits of Aerial Refinery Surveys
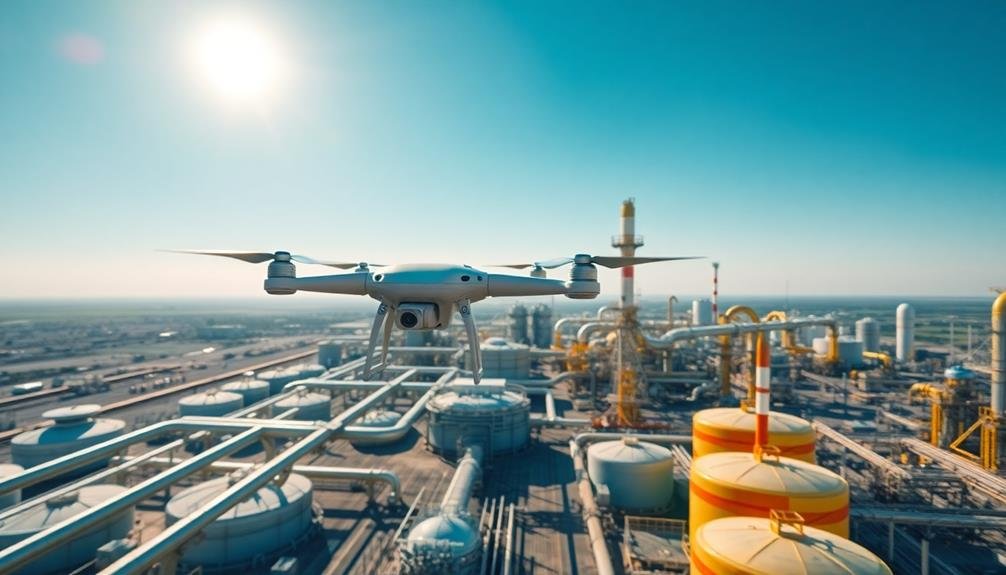
Surveyors have embraced aerial technology for refinery inspections, and it's easy to see why. Aerial surveys offer numerous advantages over traditional ground-based methods. You'll find that drones and other aerial platforms can cover large areas quickly, providing a thorough overview of the entire refinery complex. This speed translates to reduced inspection times and lower costs.
Safety is a paramount concern in refineries, and aerial surveys greatly reduce risks to personnel. You won't need to send workers into hazardous areas or at heights, minimizing potential accidents. The aerial perspective also allows you to spot issues that might be overlooked from ground level, such as roof damage or pipeline corrosion.
You'll appreciate the high-quality data collected during aerial surveys. Advanced cameras and sensors can capture detailed images and thermal readings, helping you identify potential problems before they escalate. This proactive approach to maintenance can prevent costly shutdowns and extend the life of your equipment.
Moreover, you can easily share and analyze the collected data, enabling better decision-making and collaboration among your team. With regular aerial surveys, you'll establish a thorough record of your refinery's condition over time, facilitating long-term planning and asset management.
Thermal Imaging for Leak Detection
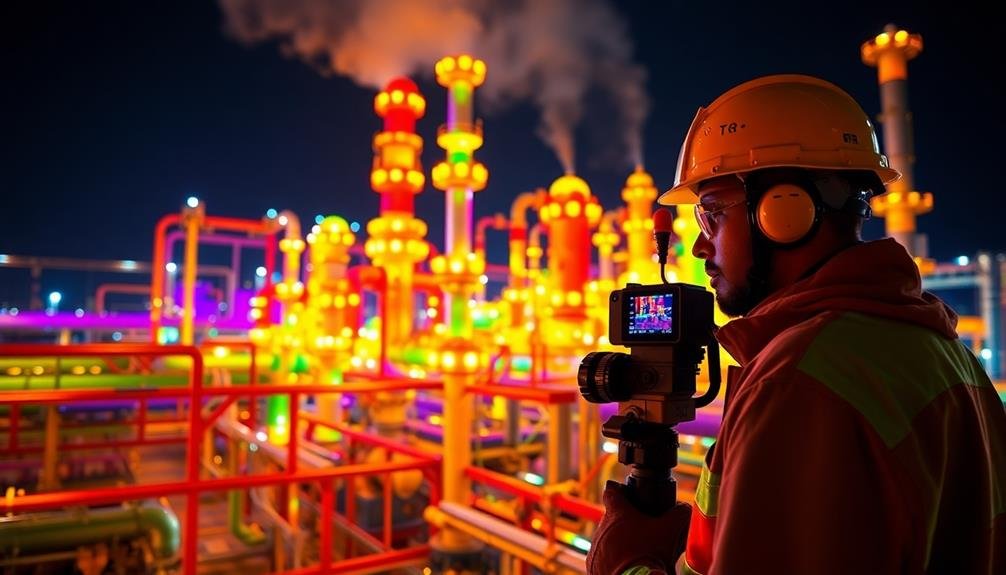
Thermal imaging technology has revolutionized leak detection in oil refineries. You'll find this cutting-edge solution markedly enhances safety and efficiency in your inspection processes. By detecting temperature variations, thermal cameras can identify leaks that are invisible to the naked eye, allowing you to address potential hazards before they escalate.
When you implement thermal imaging in your refinery inspections, you'll benefit from:
Advantages | Applications | Benefits |
---|---|---|
Early detection | Pipeline inspections | Reduced downtime |
Non-contact method | Tank surveys | Improved safety |
Large area coverage | Equipment monitoring | Cost savings |
Real-time results | Flare stack analysis | Environmental protection |
Night-time capability | Electrical inspections | Regulatory compliance |
You'll find thermal imaging particularly useful for detecting gas leaks, as escaping gases often have different temperatures than their surroundings. This technology also helps you identify insulation defects, electrical hotspots, and mechanical wear in equipment. By incorporating thermal imaging into your regular inspection routines, you'll markedly reduce the risk of accidents, minimize product loss, and optimize your refinery's overall performance. It's a smart investment that pays off in enhanced safety and operational efficiency.
AI-Powered Defect Recognition Systems
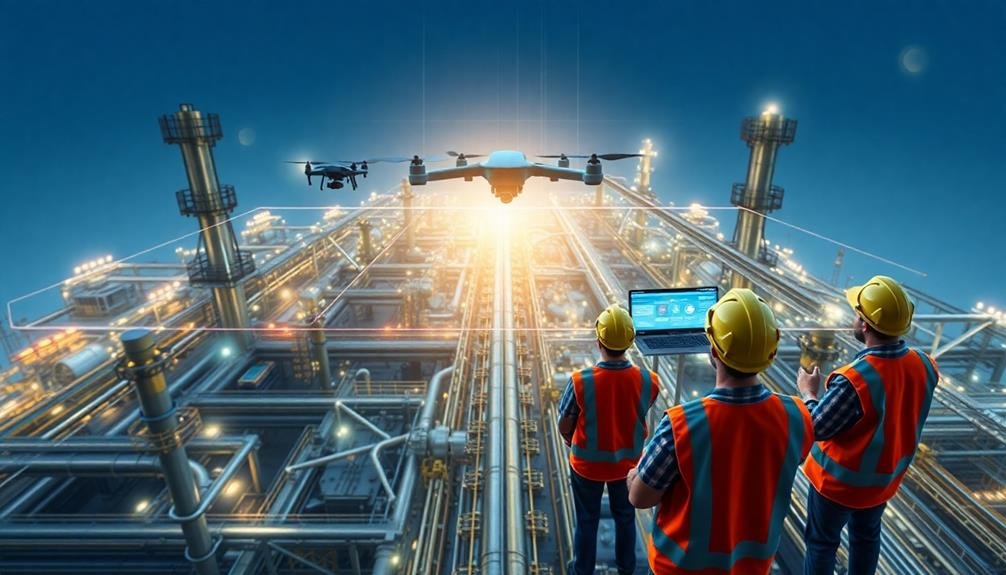
Artificial intelligence is revolutionizing defect recognition in oil refineries. You'll find that AI-powered systems can analyze complex data from various sensors and imaging devices, identifying potential issues faster and more accurately than human inspectors alone. These systems use machine learning algorithms to detect patterns and anomalies in equipment, pipelines, and structures.
As you implement AI-powered defect recognition, you'll notice improved efficiency and safety. The technology can process vast amounts of data in real-time, alerting you to potential problems before they escalate. You'll be able to prioritize maintenance tasks more effectively, reducing downtime and preventing costly failures.
These systems can integrate with existing inspection tools, such as drones and robots, enhancing their capabilities. You'll find that AI can analyze visual, thermal, and ultrasonic data simultaneously, providing a thorough view of your refinery's health.
The technology can also learn from past incidents, continuously improving its accuracy over time.
Real-Time Data Analysis Applications
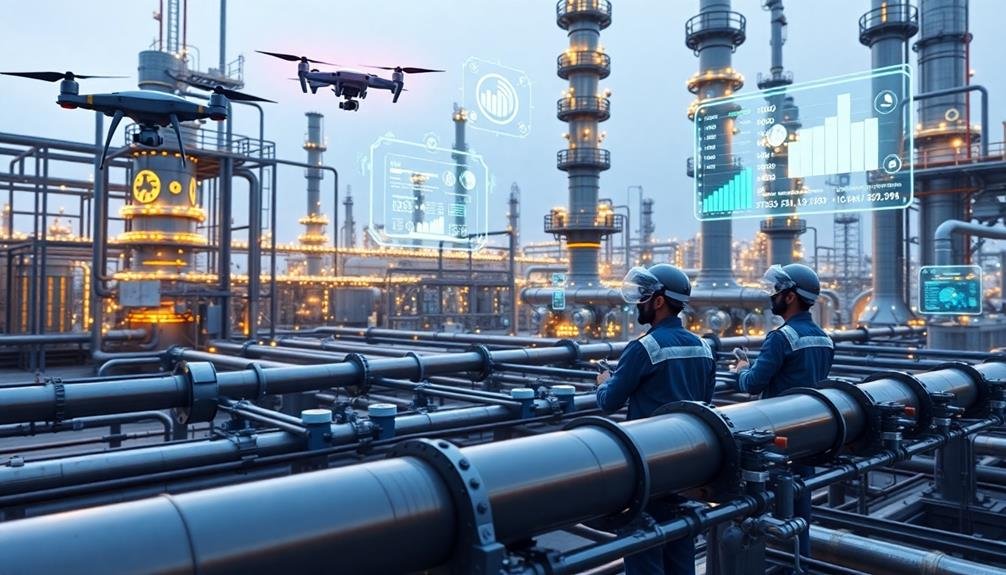
Real-time data analysis applications are transforming the landscape of oil refinery inspections. You'll find these tools revolutionizing how you monitor and evaluate refinery operations. They collect and process vast amounts of data from sensors, cameras, and other devices throughout the facility, providing instant insights into equipment performance, safety conditions, and potential hazards.
With real-time analysis, you can:
Benefit | Impact |
---|---|
Predict failures | Reduce downtime |
Identify anomalies | Prevent accidents |
Optimize processes | Increase efficiency |
Monitor emissions | Guarantee compliance |
These applications use advanced algorithms to detect patterns and trends that might escape human observation. You'll receive immediate alerts when parameters deviate from normal ranges, allowing for swift corrective action. This proactive approach notably enhances safety and operational efficiency.
Moreover, you can access this data remotely, enabling off-site experts to collaborate on complex issues. Real-time analysis also supports better decision-making by providing up-to-the-minute information on refinery conditions. As you integrate these applications into your inspection routines, you'll find they complement traditional methods, creating a more thorough and responsive safety management system.
Regulatory Compliance and Safety Improvements
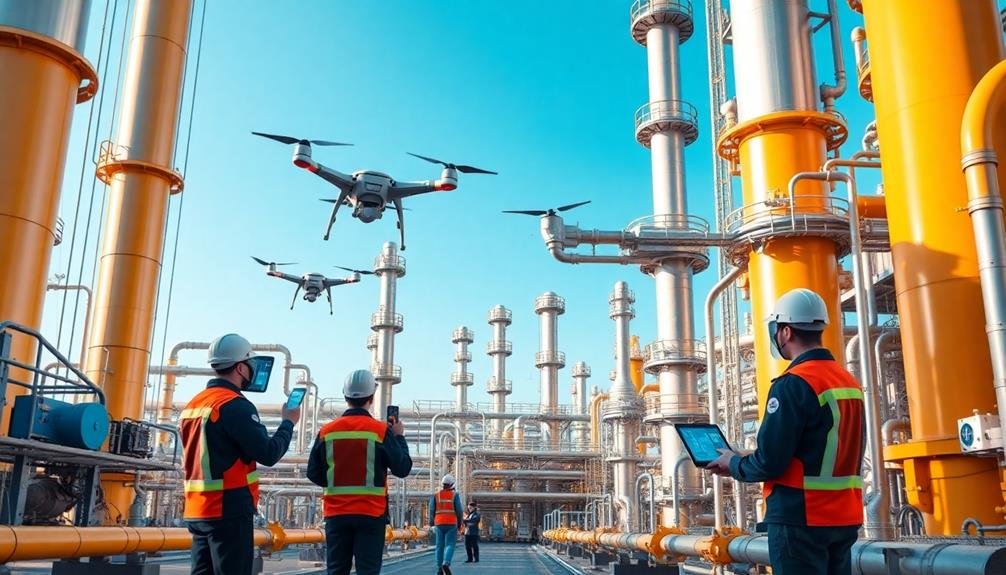
Adherence to regulatory standards is paramount in the oil refinery industry, and high-tech safety solutions are playing an essential role in ensuring compliance. You'll find that advanced technologies are revolutionizing how refineries meet and exceed safety requirements. These innovations help you identify potential hazards before they become critical issues, reducing the risk of accidents and regulatory violations.
Automated inspection systems, equipped with AI and machine learning, can detect minute defects in equipment that human inspectors might miss. You're now able to conduct more frequent and thorough inspections without increasing downtime. This leads to improved overall safety and reduces the likelihood of costly shutdowns due to equipment failure.
Moreover, you're seeing enhanced reporting capabilities that streamline the documentation process for regulatory audits. Digital platforms allow you to maintain extensive records of all inspections, maintenance activities, and corrective actions.
This not only simplifies compliance reporting but also provides valuable insights for continuous improvement of safety protocols.
Frequently Asked Questions
How Long Does It Take to Train Personnel for High-Tech Refinery Inspections?
You'll find training time varies based on the specific technology and your background. It can take anywhere from a few weeks to several months. You're looking at intensive courses covering equipment operation, data interpretation, and safety protocols.
What Are the Initial Costs of Implementing These Advanced Inspection Technologies?
You'll find initial costs for advanced inspection tech can be substantial. You're looking at expenses for equipment, software, training, and integration. Prices vary widely, but you could expect to invest several hundred thousand to millions initially.
How Often Should High-Tech Inspections Be Performed in a Typical Refinery?
You should conduct high-tech inspections at your refinery annually, at minimum. However, you'll need to increase frequency for critical equipment or areas with known issues. It's best to develop a tailored schedule based on your specific needs.
Can These Technologies Be Integrated With Existing Refinery Management Systems?
You'll find that most high-tech inspection technologies can be integrated with existing refinery management systems. They're designed to be compatible, allowing you to seamlessly incorporate new data streams into your current operational framework.
Are There Any Limitations to Using Drones in Extreme Weather Conditions?
Yes, drones face limitations in extreme weather. You'll find they struggle with strong winds, heavy rain, and extreme temperatures. They're also susceptible to lightning and can't operate in icy conditions. Battery life may decrease in cold weather too.
In Summary
You've seen how cutting-edge technology is transforming oil refinery inspections. From drones and thermal imaging to AI-powered systems, you're now equipped with tools that enhance safety, efficiency, and compliance. By embracing these innovations, you'll reduce risks, save time, and improve your refinery's overall performance. Don't hesitate to implement these high-tech solutions—they're not just the future, they're your present-day advantage in maintaining a safer, more productive refinery operation.
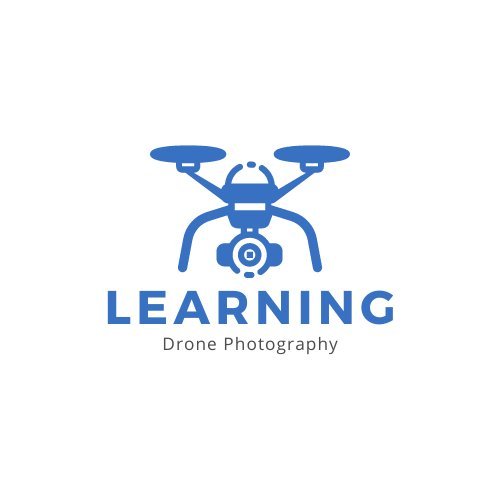
As educators and advocates for responsible drone use, we’re committed to sharing our knowledge and expertise with aspiring aerial photographers.
Leave a Reply