You're witnessing a revolution in railway safety as unmanned aerial vehicles (UAVs) transform track inspection methods. These drones offer cost-effective, efficient alternatives to manual inspections, reducing time and labor while enhancing worker safety. Equipped with high-resolution cameras and sensors, UAVs capture detailed images of tracks and infrastructure, allowing AI-powered systems to detect defects in real-time. They're reshaping maintenance strategies with continuous monitoring and rapid response protocols. Despite regulatory challenges, the future of AI-driven track monitoring looks promising, with advanced algorithms enabling predictive maintenance and seamless integration with existing railway systems. Exploring these innovations further will reveal their full potential in revolutionizing rail safety.
Key Takeaways
- UAVs significantly reduce inspection time and costs, allowing long stretches of track to be examined in hours instead of days.
- High-resolution cameras and sensors on drones capture detailed imagery, improving defect detection accuracy and data quality.
- AI-powered systems analyze drone-collected data in real-time, quickly identifying issues like cracks, corrosion, and misalignments.
- Drones enhance worker safety by minimizing on-foot inspections in hazardous areas and reducing exposure to dangerous conditions.
- UAV technology enables continuous monitoring and predictive maintenance, facilitating proactive strategies to prevent track failures.
UAV Technology in Railway Inspection
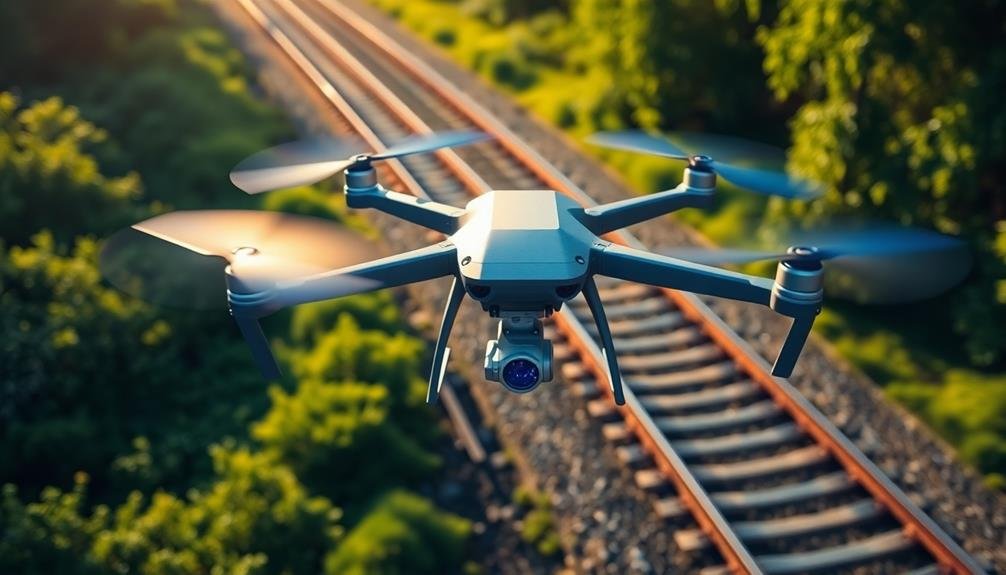
As railway networks continue to expand and age, the need for efficient inspection methods has become paramount. You'll find that Unmanned Aerial Vehicles (UAVs) are revolutionizing the way railway inspections are conducted. These drones offer a cost-effective and time-saving alternative to traditional manual inspections.
UAVs equipped with high-resolution cameras and sensors can capture detailed images of tracks, overhead lines, and surrounding infrastructure. You can use these images to identify potential issues like track defects, vegetation encroachment, or structural damage. The drones' ability to access hard-to-reach areas guarantees a more thorough inspection process.
You'll appreciate how UAV technology enhances safety for railway workers. By reducing the need for on-foot inspections in dangerous areas, you're minimizing the risk of accidents. Additionally, you can conduct inspections without disrupting train schedules, leading to improved operational efficiency.
The data collected by UAVs can be processed using artificial intelligence and machine learning algorithms. This allows you to detect patterns and predict potential failures before they occur, enabling proactive maintenance strategies.
As you implement UAV technology in railway inspection, you're not only improving safety but also optimizing resource allocation and reducing downtime.
Benefits of Drone Track Monitoring

You'll find numerous benefits when implementing drone track monitoring in railway systems. Drones offer a cost-effective and efficient way to inspect large sections of track quickly, reducing the need for manual inspections. They can access hard-to-reach areas, providing a thorough view of the entire railway network.
Drone technology enhances safety by minimizing the exposure of human inspectors to dangerous situations. You'll also notice improved accuracy in defect detection, as high-resolution cameras and sensors can capture detailed images and data. This leads to faster identification of potential issues and more timely maintenance.
Benefit | Description |
---|---|
Time Savings | Inspect long stretches of track in hours instead of days |
Cost Reduction | Lower labor costs and reduced equipment needs |
Safety Enhancement | Minimize human exposure to hazardous environments |
Data Quality | High-resolution imagery and precise measurements |
Frequency | Increase inspection frequency without disrupting operations |
Environmental Impact | Reduce carbon footprint compared to traditional methods |
Automated Defect Detection Systems

While drones excel at capturing railway data, automated defect detection systems take railway safety to the next level. These advanced systems use artificial intelligence and machine learning algorithms to analyze the vast amounts of data collected by drones and other sensors along the tracks.
You'll find that automated defect detection systems can identify a wide range of issues, from minor track irregularities to major structural problems. They're designed to detect cracks, corrosion, misalignments, and wear patterns that might escape the human eye.
By continuously monitoring the railway infrastructure, these systems can alert maintenance crews to potential hazards before they become critical.
The real-time nature of automated defect detection allows for quicker response times and more efficient maintenance scheduling. You'll appreciate how these systems can prioritize repairs based on severity, helping railway operators allocate resources more effectively.
They also reduce the need for manual inspections, minimizing human error and exposure to dangerous situations.
With automated defect detection, you're not just reacting to problems; you're proactively maintaining the railway infrastructure, ensuring safer and more reliable rail transportation for passengers and freight alike.
Real-Time Data Collection and Analysis

You'll find that real-time data collection and analysis have revolutionized railway safety.
With continuous monitoring capabilities, you're now able to track critical infrastructure and rolling stock performance around the clock.
AI-powered defect detection systems can quickly identify potential issues, enabling you to implement rapid response protocols and prevent accidents before they occur.
Continuous Monitoring Capabilities
Real-time data collection and analysis form the backbone of modern railway safety systems. With continuous monitoring capabilities, you'll find that railway operators can now detect potential issues before they escalate into serious problems.
UAV track inspection systems employ sensors and cameras that continuously scan the tracks, collecting data on rail wear, alignment, and surrounding vegetation.
You'll see these drones equipped with high-resolution cameras and LiDAR technology, allowing them to capture detailed images and 3D scans of the tracks and surrounding infrastructure. This constant stream of data is transmitted to centralized control centers, where advanced algorithms analyze it for any anomalies or deviations from normal conditions.
The continuous nature of this monitoring means you're no longer relying on periodic manual inspections. Instead, you've got a system that's always on guard, ready to alert you to developing issues.
This proactive approach considerably reduces the risk of accidents caused by track defects or obstructions. It also allows for more efficient maintenance planning, as you can prioritize repairs based on real-time condition assessments rather than fixed schedules.
Ai-Powered Defect Detection
Through the integration of artificial intelligence, railway safety systems have reached new heights in defect detection capabilities. You'll find that AI-powered algorithms can now analyze vast amounts of data collected by UAVs in real-time, identifying potential issues that might escape human observers.
These advanced systems can detect minute cracks, wear patterns, and irregularities in track geometry with unprecedented accuracy. They're capable of learning from historical data, improving their detection abilities over time. You'll see AI systems flagging potential problems before they become critical, allowing for proactive maintenance and reducing the risk of accidents.
AI-powered defect detection isn't limited to just track conditions. It can also monitor overhead lines, signaling equipment, and surrounding vegetation. You'll benefit from its ability to prioritize maintenance tasks based on the severity and potential impact of detected issues.
As you implement these systems, you'll notice a significant reduction in manual inspection time and costs. The AI's continuous learning capabilities mean you're always working with the most up-to-date defect detection protocols, ensuring your railway network remains at the forefront of safety innovation.
Rapid Response Protocols
While AI-powered defect detection provides essential insights, the true power of railway safety lies in how quickly and effectively you can respond to identified issues. Rapid response protocols guarantee that your team can take immediate action when potential hazards are detected. These protocols integrate real-time data collection and analysis, enabling you to make informed decisions swiftly.
You'll find that implementing a structured rapid response system considerably reduces downtime and enhances overall safety. Here's a breakdown of key elements in an effective rapid response protocol:
Phase | Action | Time Frame |
---|---|---|
Alert | Notify relevant personnel | Immediate |
Assessment | Evaluate severity and impact | 5-15 minutes |
Mobilization | Deploy response team | 15-30 minutes |
Resolution | Implement corrective measures | Varies by issue |
Cost-Efficiency of UAV Inspections
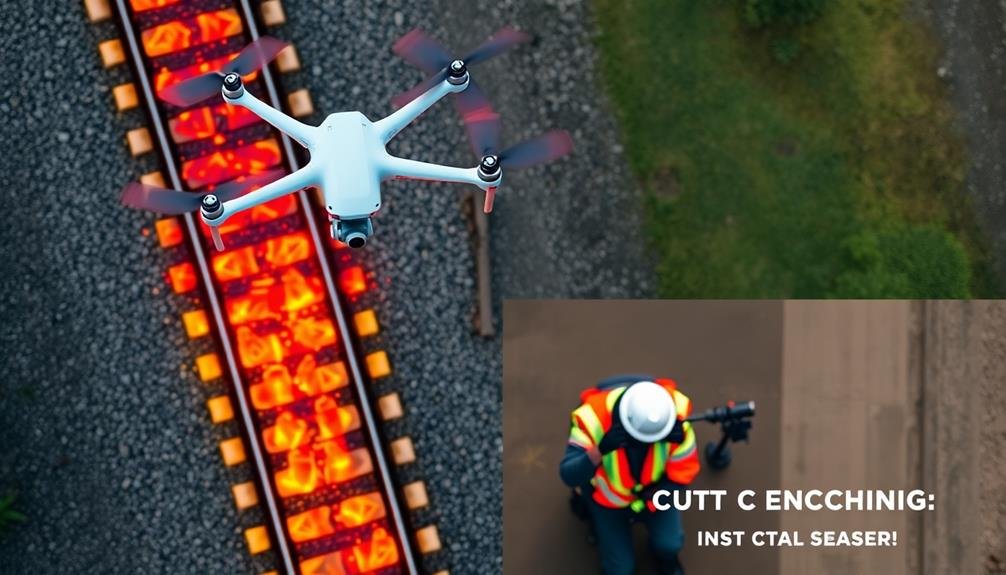
As railway operators seek to streamline their inspection processes, UAV (unmanned aerial vehicle) technology has emerged as a cost-effective solution. You'll find that these drones can greatly reduce the time and manpower required for track inspections, leading to substantial cost savings.
By deploying UAVs, you're able to cover large areas quickly and efficiently, minimizing the need for on-site personnel and reducing safety risks associated with manual inspections.
The cost-efficiency of UAV inspections is evident in several ways:
- Reduced labor costs: You'll need fewer staff members to operate drones compared to traditional inspection teams.
- Decreased downtime: UAVs can inspect tracks without disrupting regular train schedules, minimizing revenue loss.
- Lower equipment expenses: Drones are more affordable than specialized inspection vehicles and require less maintenance.
You'll also benefit from the ability to conduct more frequent inspections without incurring considerable additional costs. This increased inspection frequency allows you to identify potential issues earlier, preventing costly repairs and enhancing overall safety.
Furthermore, the high-quality data collected by UAVs enables you to make more informed decisions about maintenance priorities, optimizing your resource allocation and further improving cost-efficiency.
Safety Improvements for Maintenance Crews
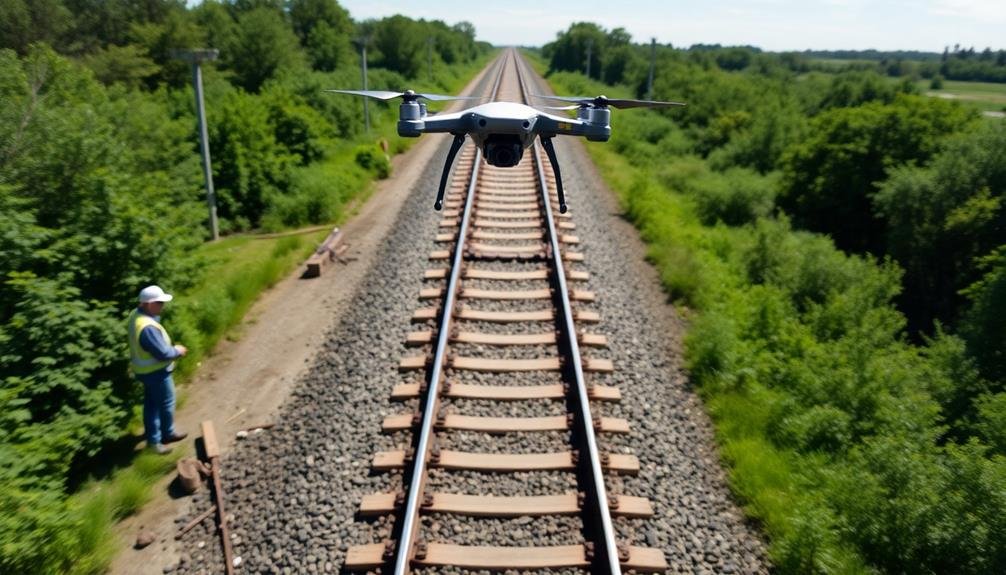
Safety improvements for maintenance crews have become a top priority in railway operations. You'll find that modern technology and innovative practices are revolutionizing the way maintenance teams work on tracks. By implementing remote monitoring systems, you're reducing the need for physical inspections, minimizing crew exposure to dangerous situations. These systems use sensors to detect track abnormalities, allowing you to address issues before they become critical.
You're also adopting personal protective equipment (PPE) with built-in communication devices, enhancing crew safety and coordination. This equipment includes high-visibility clothing with integrated GPS trackers, ensuring you can quickly locate and assist workers in case of emergencies.
Additionally, you're utilizing mobile apps that provide real-time updates on train schedules and track conditions, helping you plan maintenance activities more safely and efficiently.
To further protect your crews, you're implementing automated warning systems that alert workers of approaching trains well in advance. These systems use a combination of sensors, cameras, and AI to detect oncoming trains and provide ample time for crews to clear the tracks.
Environmental Impact of Drone Inspections

Implementing drone inspections for railway safety has considerably reduced the environmental impact of traditional inspection methods. You'll find that drones consume far less energy than traditional vehicles used for track inspections. They don't emit greenhouse gases or other pollutants during operation, making them a cleaner alternative.
Additionally, drones minimize the disturbance to wildlife habitats along railway corridors.
When you compare drone inspections to conventional methods, you'll notice significant environmental benefits:
- Reduced fuel consumption: Drones use rechargeable batteries, eliminating the need for fossil fuels.
- Decreased noise pollution: UAVs operate quietly, causing less disturbance to nearby communities and wildlife.
- Minimal ground impact: Drones don't require physical access to tracks, preserving surrounding vegetation and soil.
You'll also appreciate that drone inspections reduce the need for heavy machinery and vehicles on-site. This means less soil compaction and vegetation damage along railway lines.
Moreover, drones can access hard-to-reach areas without disturbing sensitive ecosystems. By adopting drone technology, you're contributing to more sustainable railway maintenance practices and helping preserve the environment for future generations.
Regulatory Challenges and Compliance

You'll find that UAV regulations for railway inspections are constantly evolving, requiring operators to stay updated on the latest rules.
Compliance with these changing regulations can be challenging, as you must adapt your inspection procedures and equipment accordingly.
Safety certification processes for drone-based railway inspections are becoming more rigorous, demanding thorough training and documentation from your team.
Evolving UAV Regulations
Regulation of unmanned aerial vehicles (UAVs) in railway safety is a rapidly evolving field. As you navigate this dynamic landscape, you'll find that regulatory bodies are constantly updating their guidelines to keep pace with technological advancements.
You'll need to stay informed about the latest rules governing UAV operations near railway infrastructure.
To comply with current regulations, you must:
- Obtain proper licensing and certifications for your UAV pilots
- Register your drones with relevant authorities
- Adhere to flight restrictions and no-fly zones around railways
You'll also need to take into account privacy concerns and data protection laws when capturing imagery during track inspections.
It's essential to implement robust security measures to prevent unauthorized access to sensitive information collected by your UAVs.
As regulations continue to evolve, you'll face challenges in adapting your operations to meet new requirements. You may need to invest in updated equipment or modify your inspection procedures.
Safety Certification Processes
Safety certification processes in the railway industry present a complex web of regulatory challenges and compliance requirements. As you navigate this landscape, you'll encounter stringent standards set by bodies like the Federal Railroad Administration (FRA) and European Union Agency for Railways (ERA).
These agencies demand rigorous testing and documentation to guarantee your UAV inspection systems meet safety benchmarks. You'll need to demonstrate your technology's reliability, accuracy, and fail-safe mechanisms. This involves extensive field trials, data validation, and risk assessments.
You must also address cybersecurity concerns, proving your systems are protected against potential hacking or interference. Compliance isn't a one-time effort; it's an ongoing process.
You'll face regular audits and may need to recertify as regulations evolve. Staying ahead of these changes is essential. Consider forming partnerships with regulatory experts or joining industry working groups to anticipate shifts in the regulatory landscape.
Future of AI-Powered Track Monitoring

The future of AI-powered track monitoring looks promising for railway safety. You'll see advanced algorithms processing vast amounts of data from various sensors, cameras, and drones to detect potential issues before they become critical. These AI systems will learn from historical data and continuously improve their accuracy, reducing false alarms and increasing overall efficiency.
As you consider the potential of AI-powered track monitoring, imagine:
- Autonomous drones flying along tracks, using high-resolution cameras and LiDAR to capture detailed 3D images of rail infrastructure.
- AI algorithms analyzing these images in real-time, identifying minute cracks, wear patterns, and misalignments invisible to the human eye.
- Predictive maintenance schedules automatically generated based on AI-driven risk assessments, optimizing resource allocation and minimizing disruptions.
You'll find that AI-powered systems will integrate with existing railway management platforms, providing an all-encompassing view of track conditions across entire networks. This integration will enable faster decision-making and more effective maintenance strategies.
As AI technology continues to evolve, you can expect even more sophisticated monitoring capabilities, such as AI-powered robots conducting hands-on inspections and repairs, further enhancing railway safety and operational efficiency.
Integration With Existing Railway Systems

You'll find that integrating new railway safety innovations with existing systems requires careful consideration of data sharing protocols.
As you implement real-time monitoring solutions, you're connecting advanced sensors and AI systems with traditional railway infrastructure.
This integration allows for automated maintenance scheduling, ensuring timely repairs and reducing downtime across the network.
Data Sharing Protocols
Numerous railway systems worldwide rely on outdated data-sharing protocols, creating barriers to seamless integration of new safety innovations. You'll find that modernizing these protocols is essential for implementing UAV track inspection technologies effectively.
By adopting standardized data formats and communication methods, you can guarantee that information flows smoothly between UAVs, control centers, and existing railway management systems.
To achieve this, you'll need to focus on three key areas:
- Developing secure, real-time data transmission protocols
- Creating standardized data formats for easy interpretation across different systems
- Implementing robust encryption methods to protect sensitive information
You'll discover that these improvements not only enhance UAV track inspection capabilities but also pave the way for future innovations.
By establishing a foundation of efficient data sharing, you're enabling faster response times to potential safety issues and more accurate decision-making processes.
Remember, the success of UAV track inspections heavily relies on your ability to seamlessly integrate the gathered data with existing railway systems.
Prioritizing the development of advanced data-sharing protocols will greatly boost the overall effectiveness of your railway safety initiatives.
Real-Time Monitoring Integration
Integrating real-time monitoring systems with existing railway infrastructure presents both challenges and opportunities for enhancing safety and efficiency. You'll need to take into account how UAV-based track inspection data can seamlessly interface with current railway management systems. This integration allows for immediate updates on track conditions, potential hazards, and maintenance needs.
To achieve successful integration, you'll want to focus on:
Integration Aspect | Challenge | Solution |
---|---|---|
Data Format | Incompatible formats | Develop standardized formats |
Communication | Limited connectivity | Implement robust wireless networks |
Processing Speed | Large data volumes | Utilize edge computing |
Security | Cyber threats | Employ advanced encryption |
User Interface | Complex data visualization | Design intuitive dashboards |
By addressing these aspects, you'll create a more responsive and proactive railway safety system. Real-time monitoring integration enables you to:
- Detect issues before they escalate
- Optimize maintenance schedules
- Improve resource allocation
- Enhance decision-making processes
- Increase overall system reliability
Automated Maintenance Scheduling
Building on the real-time monitoring integration, automated maintenance scheduling represents the next step in enhancing railway operations. You'll find that this system seamlessly integrates with existing railway infrastructure, using data collected from UAV inspections and real-time sensors to prioritize and schedule maintenance tasks efficiently.
By leveraging machine learning algorithms, the automated system analyzes historical data, current track conditions, and predicted wear patterns to generate ideal maintenance schedules. This proactive approach allows you to address potential issues before they escalate, reducing downtime and improving overall safety.
The automated maintenance scheduling system offers several key benefits:
- Real-time updates on track conditions, allowing you to visualize problem areas and prioritize repairs.
- Predictive maintenance alerts, enabling you to allocate resources more effectively and reduce unexpected breakdowns.
- Enhanced workforce management, ensuring that your maintenance teams are deployed strategically and efficiently.
You'll notice a significant improvement in your railway's operational efficiency as the automated system continually refines its scheduling based on new data and feedback.
This integration not only enhances safety but also reduces costs associated with unnecessary maintenance and potential service disruptions.
Case Studies: Successful UAV Implementations

Unmanned Aerial Vehicles (UAVs) have soared to new heights in railway safety, with several successful implementations showcasing their potential.
You'll find that Network Rail in the UK has been at the forefront of this technology, using drones to inspect hard-to-reach areas of their rail network. They've reported significant time and cost savings, as well as improved safety for inspection teams.
In Japan, the East Japan Railway Company has implemented UAVs equipped with high-resolution cameras and thermal imaging sensors. These drones have successfully detected minute cracks and heat anomalies in rail infrastructure, preventing potential accidents before they occur.
You'll also see success in the United States, where BNSF Railway has obtained FAA approval for beyond-visual-line-of-sight (BVLOS) drone operations. This allows them to inspect vast stretches of track quickly and efficiently, especially in remote areas.
In Australia, Rio Tinto's autonomous rail network utilizes drones for regular inspections of its 1,700 km track. This integration of UAVs with their already automated system has further enhanced safety and operational efficiency.
These case studies demonstrate that UAVs aren't just a futuristic concept but a present-day solution for improving railway safety and maintenance practices.
Frequently Asked Questions
How Do UAVS Navigate Through Tunnels and Under Bridges During Inspections?
You'll find that UAVs use specialized sensors like LiDAR and ultrasonic to navigate tunnels and bridges. They're equipped with powerful lights and can fly autonomously using pre-programmed routes. Some even use AI for obstacle avoidance in tight spaces.
What Are the Battery Life Limitations for Drones Used in Railway Inspections?
You'll find that drone battery life for railway inspections typically ranges from 20-40 minutes. It's limited by factors like payload, weather, and flight speed. You'll need to plan multiple battery swaps for longer inspections.
Can UAVS Detect Potential Security Threats or Trespassers Along Railway Tracks?
Yes, UAVs can detect security threats and trespassers along railway tracks. You'll find they're equipped with high-resolution cameras and thermal sensors, allowing them to spot suspicious activities or unauthorized individuals in real-time, even in low-light conditions.
How Do Weather Conditions Affect the Accuracy of Drone-Based Track Inspections?
Weather conditions can considerably impact your drone-based track inspections. You'll find that rain, snow, and fog reduce visibility and accuracy. Strong winds can affect flight stability. Extreme temperatures may also interfere with drone performance and sensor readings.
Are There Plans to Develop Autonomous Drones for Continuous Railway Monitoring?
Yes, there are plans for autonomous drones in railway monitoring. You'll see more self-flying drones patrolling tracks 24/7, using AI to detect issues. They'll relay real-time data, improving safety and reducing human inspection needs.
In Summary
You've seen how UAVs are transforming railway safety. They're faster, cheaper, and more efficient than traditional methods. With automated defect detection and real-time analysis, you'll catch issues before they become dangerous. While regulatory hurdles exist, the future's bright for AI-powered track monitoring. As you integrate these systems, you'll revolutionize railway maintenance. Remember the successful case studies—they prove that UAV technology isn't just a possibility, it's the way forward for safer, smarter railways.
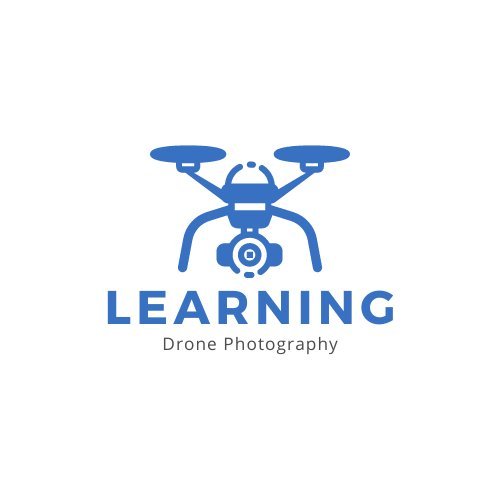
As educators and advocates for responsible drone use, we’re committed to sharing our knowledge and expertise with aspiring aerial photographers.
Leave a Reply