Wind turbine inspections need advanced flying robots to overcome the limitations of traditional methods. You'll find that drones equipped with high-tech sensors can access hard-to-reach areas quickly and safely, reducing risks for technicians. They capture detailed images and thermal data, allowing for thorough analysis of turbine components. These robots complete inspections faster, cutting costs and increasing productivity. They also enhance safety by minimizing human exposure to hazards like falls and extreme weather. With real-time data processing and AI-powered analysis, you'll get more accurate and timely insights for maintenance decisions. Discover how these flying marvels are transforming the wind energy industry.
Key Takeaways
- Advanced flying robots eliminate safety risks associated with manual inspections of tall wind turbines.
- Drones equipped with high-resolution cameras and sensors capture detailed imagery of hard-to-reach turbine components.
- Flying robots significantly reduce inspection time and costs compared to traditional methods.
- AI-powered drones provide real-time data processing and analysis for immediate issue detection.
- Robotic inspections enable more frequent and comprehensive monitoring, improving overall wind farm maintenance strategies.
Challenges of Traditional Inspection Methods

The traditional methods of inspecting wind turbines come with a host of challenges. You'll find that these inspections often involve technicians climbing up tall towers or using ground-based telescopes, both of which have significant limitations.
When climbing, technicians face safety risks and can only inspect a limited number of turbines per day. This method is time-consuming, expensive, and weather-dependent.
Ground-based telescopes, while safer, can't provide detailed images of blade surfaces or nacelles. You'll miss critical defects that are only visible up close.
Crane-based inspections offer better visibility but are costly and logistically complex. They're also impractical for offshore wind farms.
You'll encounter additional hurdles with these methods. They often require shutting down turbines, leading to lost energy production. Weather conditions frequently delay inspections, causing scheduling nightmares.
Data collection is manual and prone to human error, making it difficult to track changes over time.
Moreover, you can't easily inspect hard-to-reach areas like the underside of blades or the interior of nacelles. These limitations mean you might miss early signs of wear, leading to more extensive and expensive repairs down the line.
Advanced Capabilities of Flying Robots

Flying robots, specifically drones, offer a revolutionary solution to these inspection challenges. They're equipped with high-resolution cameras and thermal imaging sensors, allowing you to capture detailed images and videos of turbine blades, nacelles, and towers. You'll be able to detect even the smallest cracks, erosion, or thermal anomalies that might escape the human eye.
These drones can navigate complex wind farm environments with precision, using GPS and obstacle avoidance technology. You'll find they can access hard-to-reach areas of turbines quickly and safely, reducing inspection time and eliminating the need for dangerous manual inspections.
Advanced AI and machine learning algorithms can process the collected data in real-time, providing you with instant analysis and actionable insights. This rapid assessment allows for immediate decision-making on maintenance needs, potentially preventing costly breakdowns.
Moreover, drones can operate in various weather conditions and at different times of day, giving you flexibility in scheduling inspections. They can also cover large areas quickly, making them ideal for inspecting multiple turbines in a single operation.
With these capabilities, you'll greatly improve the efficiency and effectiveness of your wind turbine inspection processes.
Cost-Efficiency and Time Savings

While traditional inspection methods can be costly and time-consuming, flying robots offer significant cost-efficiency and time savings for wind turbine inspections.
You'll find that these advanced drones can complete inspections in a fraction of the time it takes human technicians to manually inspect turbines. They don't require expensive scaffolding or crane rentals, reducing setup costs dramatically.
You'll appreciate how flying robots can inspect multiple turbines in a single day, increasing productivity and minimizing downtime.
They're not limited by weather conditions or safety concerns that often delay manual inspections. With their ability to access hard-to-reach areas quickly, you'll detect issues earlier, potentially saving thousands in repair costs.
You'll also benefit from reduced labor costs, as fewer personnel are needed on-site.
The high-quality data collected by these robots allows for more accurate assessments, reducing the need for follow-up inspections. Over time, you'll see substantial savings in your maintenance budget.
Additionally, the decreased reliance on human inspectors reduces workplace accidents and associated costs.
Safety Enhancements for Inspection Personnel

Safety harnesses and helmets are no longer the only line of defense for wind turbine inspectors. Advanced flying robots now offer a significant boost to personnel safety during inspections. You'll find that these drones can access hard-to-reach areas of turbines, reducing the need for inspectors to scale dangerous heights or navigate treacherous terrain.
By using drones, you're minimizing human exposure to potential falls, electrical hazards, and extreme weather conditions. They can operate in high winds and inspect blade edges where human access is risky. You'll appreciate how drones can capture detailed images and data without putting inspectors in harm's way.
Moreover, you're reducing the risk of repetitive strain injuries that often plague climbers who perform manual inspections. Drones can carry out continuous inspections without fatigue, ensuring consistent quality throughout the process.
You'll also notice a decrease in accidents related to falling objects or equipment failure, as fewer tools and personnel are required on-site.
Data Collection and Analysis Improvements

How has drone technology revolutionized data collection for wind turbine inspections? You'll find that drones equipped with high-resolution cameras and thermal imaging sensors can capture detailed images and videos of turbine blades, nacelles, and towers.
These flying robots collect data much faster and more thoroughly than traditional methods, allowing you to inspect multiple turbines in a single day.
You'll appreciate how drones can access hard-to-reach areas, providing a 360-degree view of turbine components. They capture close-up images of potential defects, such as cracks, erosion, or lightning damage, that might be missed by ground-based inspections.
The thermal imaging capabilities let you detect hidden issues like delamination or water ingress.
With advanced software, you can process and analyze the collected data quickly. AI-powered algorithms can identify and categorize defects automatically, saving you time and improving accuracy.
You'll receive thorough reports with detailed imagery, allowing for more informed maintenance decisions. This data-driven approach enables predictive maintenance strategies, helping you optimize turbine performance and extend their lifespan while reducing downtime and repair costs.
Frequently Asked Questions
How Do Flying Robots Navigate Around Wind Turbines in Extreme Weather Conditions?
You'll find flying robots use advanced sensors and AI to navigate turbines in harsh weather. They'll adjust for wind, utilize obstacle avoidance, and employ stabilization systems. You'd see them maintain precise positioning and adapt to changing conditions.
What Regulations Govern the Use of Drones for Wind Turbine Inspections?
You'll need to comply with FAA regulations for commercial drone use. These include getting a Part 107 license, registering your drone, and following operational rules like maintaining visual line of sight and avoiding restricted airspace.
Can Flying Robots Detect Internal Structural Issues in Wind Turbine Blades?
You'll find that advanced flying robots can detect internal structural issues in wind turbine blades. They're equipped with thermal cameras and ultrasonic sensors that penetrate the blade's surface, revealing hidden defects like delamination or moisture ingress.
How Often Should Wind Turbine Inspections Be Conducted Using Flying Robots?
You should conduct wind turbine inspections using flying robots at least annually. However, you'll need to increase frequency based on factors like turbine age, environmental conditions, and previous issues. It's best to consult with experts for your specific situation.
Are There Any Environmental Concerns Associated With Using Drones Near Wind Farms?
You'll find some environmental concerns with drone use near wind farms. They can disturb wildlife, especially birds and bats. Noise pollution's another issue. You'll need to follow regulations and best practices to minimize these impacts.
In Summary
You've seen how advanced flying robots revolutionize wind turbine inspections. They overcome traditional challenges, offering superior capabilities and cost-efficiency. These drones enhance safety for personnel and vastly improve data collection and analysis. As the wind energy sector grows, you'll find these high-tech solutions becoming indispensable. By embracing this technology, you're not just optimizing inspections; you're propelling the industry towards a more efficient, safer future in renewable energy maintenance.
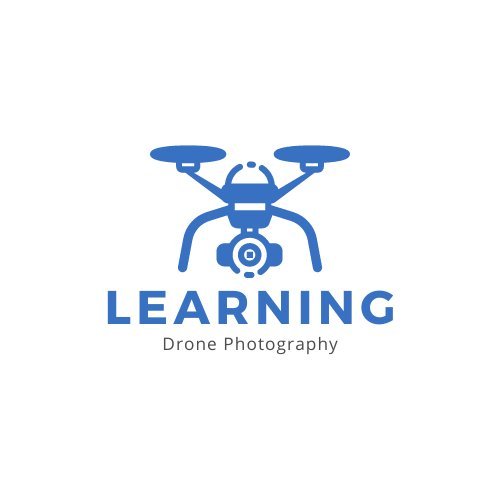
As educators and advocates for responsible drone use, we’re committed to sharing our knowledge and expertise with aspiring aerial photographers.
Leave a Reply